On most construction projects, the general contractor is responsible for providing professional services that assist all the contractors on site in performing their work. These professional services include supervision, temporary utilities, site security, safety controls, permits, and several other categories of costs. It’s important for general contractors to include these costs in their proposals, as they can add up quickly and are necessary for the project to be completed.
In this article, we are going to look at what general construction conditions are, how they differ from general requirements and overhead costs, and how to calculate them for your next project.
What are general conditions?
General conditions can be found in three places on a construction project: the project contract, the specifications, and the project costs. In each of these locations, general conditions mean something slightly different.
In the project contract, the general conditions are contract terms that define the relationship between the owner, contractor, and possibly the architect. Provisions include the roles and responsibilities of each of the construction contract parties, important dates such as the commencement date and substantial completion, how to handle delays, payment terms, changes to the work, and how claims and disputes will be handled. The most widely used version of general conditions is that provided by the AIA. Most of the contract templates the AIA provides use the A201 General Conditions as the basis for the contract terms.
In a project’s specifications, the general conditions or general requirements provide information to contractors about project administration roles, responsibilities, and processes. For example, the requirements include information on project meetings, submittal processing, how change orders will be handled, etc. These detailed terms are project specific and often provide more guidance than the contract general conditions, which may be boilerplate.
As far as project costs go, general conditions represent the costs required to provide the infrastructure and resources for the general contractor and trade subcontractors to complete all phases of a construction project. These costs are usually carried out by the general contractor for the benefit of everyone on the project.
What types of costs are included in general conditions?
The project costs that are included in general conditions are generally made up of four categories: site management, project management, material handling, and trash removal.
Site management costs include providing the infrastructure for the project. This includes providing temporary utilities, such as electricity and water, temporary offices for meetings, portable toilets, erosion control, temporary fencing, lighting, building permits, safety controls, etc. These items are required for everyone on the specfic job to perform their work safely.
Project business management costs include the labor required by the general contractor to oversee and assist trade contractors in completing the work. A general contractor’s team may consist of a project manager, project engineer, superintendent, and foreman. The GC’s supervision is required to ensure that the project meets the construction contract documents, comprised of the drawings and specifications.
Material handling costs include equipment rental and labor to accept delivery of, protect, and stage materials and products for the project. These costs may also include security to protect materials from theft or vandalism.
Finally, trash removal is considered part of the general conditions of a project. Usually, the general contractor is responsible for providing dumpsters and recycling bins for debris generated by the project. In addition, the general contractor may provide labor to clean the site daily to prevent safety hazards and keep the project looking professional.
General conditions vs general requirements
As was mentioned above, the general conditions on a project are the costs required by the general contractor to create and maintain a safe and efficient job site. They include project supervision, temporary and permanent utilities, equipment rental, fencing, security, permits, etc.
The general requirements are provided in the specifications under CSI Division 1 and detail the methods and processes that will be used to complete the project. They define processes for submittals, requests for information (RFIs), change order review, etc.
Are general conditions overhead?
General conditions are not considered overhead. They are costs attached to a specific project that helps the entire project team complete the work required by the contract. Overhead costs are the general costs of doing business that is incurred by all contractors and is not tied to a specific project.
General conditions are costs incurred that lead to project success, while overhead are costs incurred that lead to company success. In addition, a contractor is responsible for paying overhead costs whether a job is in progress or not, while general conditions costs are paid for a specific job.
How to calculate general conditions costs
The best way to calculate general conditions costs is to look at past cost data. By reviewing similar projects of similar duration, you’ll be able to accurately estimate your costs on the current project. Be sure to add room for price increases, especially in these turbulent economic times.
If you don’t have past project data to look at, you’ll have to price each part of the general conditions separately. General conditions are usually priced for the duration of the project, so knowing how long the project is expected to take is key to determining these costs. For example, let’s say a portable toilet cost $100 a month. If the project is expected to take six months, you can allocate $600 for this service. But if the project actually takes nine months, you’ll either absorb the additional $300 or charge the owner through a change order, depending on the cause of the delay.
Once you’ve determined the anticipated schedule for the project, you can estimate your general conditions costs. List each type of cost you’ll need to provide on the project, calculate an approximate monthly project cost, and multiply it by the expected duration of the project. You may want to add an additional amount to each item for contingency or in case the project takes longer than expected.
General conditions are services, equipment, and materials that general contractors provide to ensure that projects are completed as drawn and specified within the project’s schedule. They include costs related to site management, project management, materials handling, and trash removal. General conditions costs are different than general requirements and company overhead costs. The best way to estimate general conditions costs is to base them on prior project data. If you don’t have that, you can list each project cost and multiply it by the duration of the project. It’s important to accurately estimate and manage these costs, as they can quickly go over budget and affect project profitability. Visit PlanHub for all your construction general conditions needs.
Resources
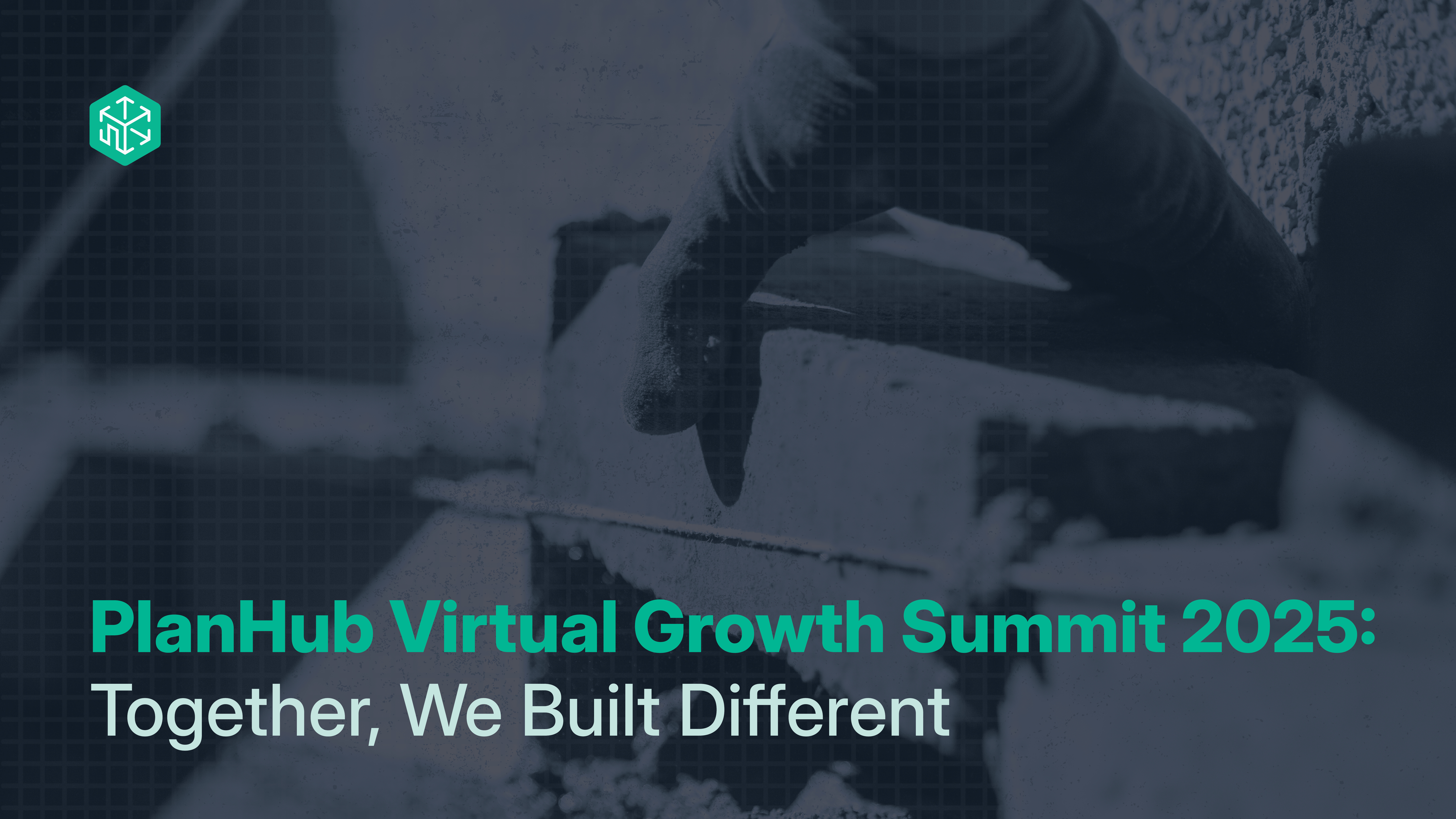
PlanHub Virtual Growth Summit 2025: Together, We Built Different
On June 24th, 2025, we hosted our first-ever Virtual Growth Summit: Built Different and let’s just say, it lived up to the name. This summit
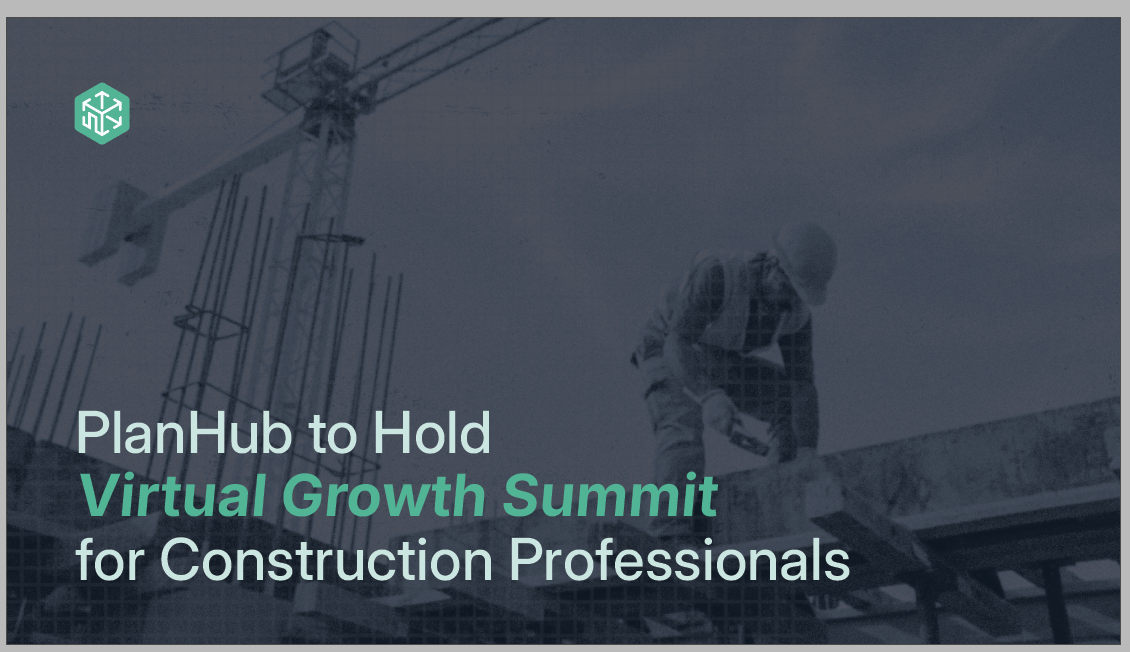
PlanHub To Hold Virtual Growth Summit for Construction Professionals
WEST PALM BEACH, Fla., June 12, 2025 /PRNewswire-PRWeb/ — PlanHub, the premier preconstruction management solution for commercial construction professionals, is proud to announce Virtual Growth
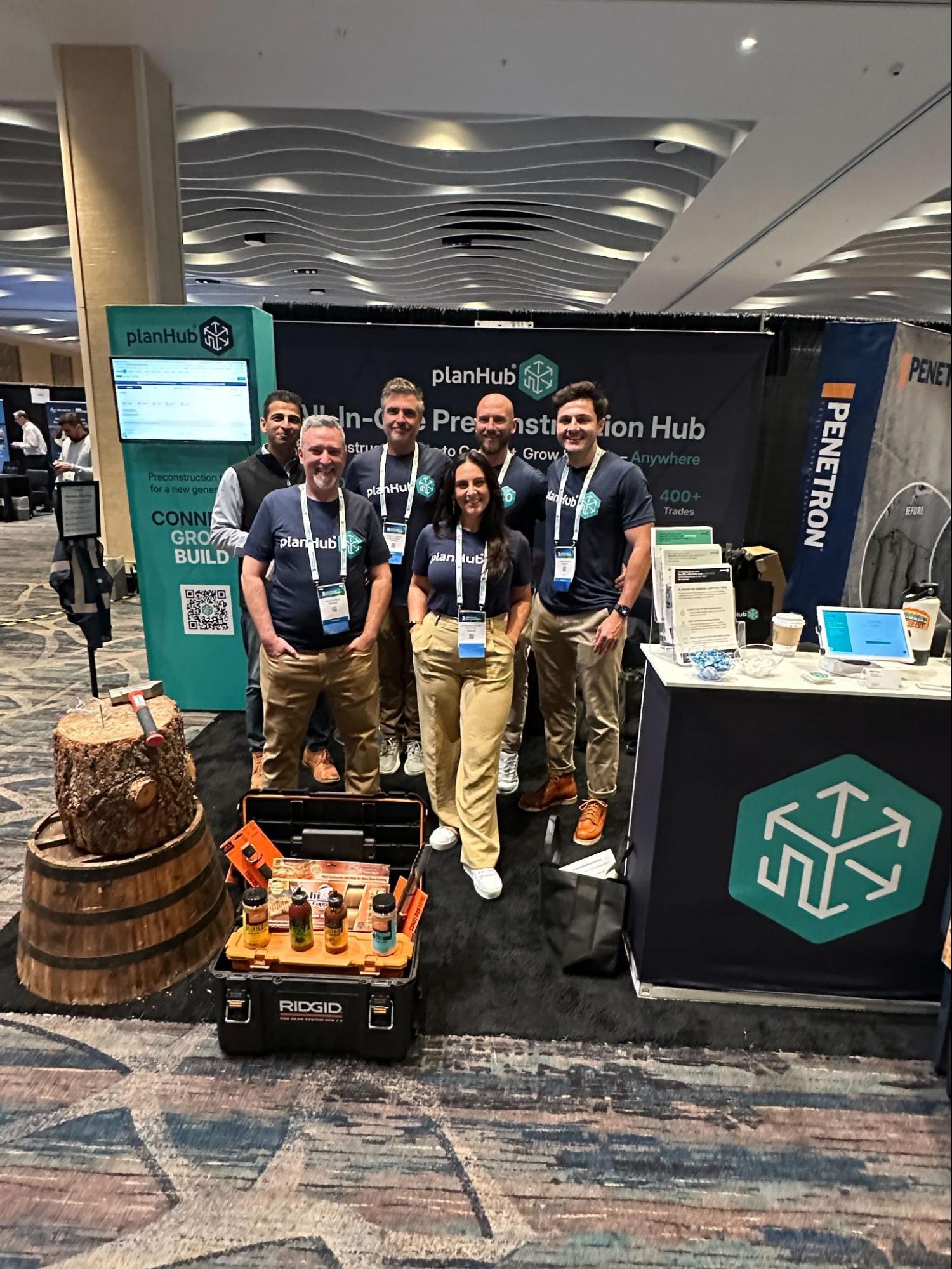
Building Better, Together: Our Unforgettable Experience at the 2025 Advancing Preconstruction Conference
Last week, five of us from PlanHub flew in from all across the U.S.—California, Arizona, Utah, and Wisconsin—to meet up in San Diego for one